Mold development to mass production
❖ Mold Development Process
- Customer provides sample
- The customer provides a sample for mold development based on their requirements.
- Estimate the mold cost based on the sample and provide a quotation to the customer.
- Customer provides ideas
- Confirm the ideas, appearance, and performance requirements for the product with the customer or the marketing department.
- Evaluate the feasibility of mold development and mass production for the product.
- Estimate the mold cost and provide a quotation to the customer.
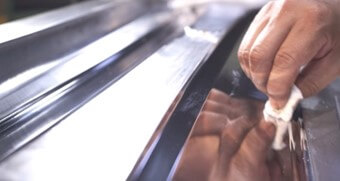
Price nego Contract
- Negotiate a price that is acceptable to both parties.
- Sign the contract.
Mold Design
- Use 3D modeling software (CATIA) to create the product model; perform mold flow simulation to predict issues and optimize the design.
- Design the mold's cavity, core, runner, gate, cooling, and ejector systems, and determine the mold structure type.
- Create 2D manufacturing drawings and 3D mold design models, then submit them to the customer for confirmation before entering the manufacturing stage.
Mold Manufacturing
- Select the appropriate mold steel and perform heat treatment according to the requirements to improve hardness and wear resistance.
- Rough machining, precision machining, surface treatment, etc.
- Assemble the mold components into a complete mold.
Quality Inspection
- Inspecting Mold Dimensions to Ensure Compliance with Design
- Testing Mold Functionality and Stability
- Checking for Surface Defects on the Mold
Mold Trial Adjustment
- Install the mold onto the injection molding machine for trial, and check if the injected product has any defects.
- Analyze the trial product and modify the injection parameters or mold structure if necessary.
- Conduct multiple trials and optimize the mold to meet customer requirements.
Mold Acceptance
- Submit samples to the customer for inspection of appearance, dimensions, and functionality.
- Sign the acceptance documents after customer approval.
- ※If the customer confirms it as NG, re-trial and adjustments will be required.
Mass Production Preparation
- After mold acceptance, transfer it to the production department for mass production.
- Perform regular maintenance and upkeep of the mold to extend its service life.
Production Process
- Proceed production trial and verifying compliance with quality standards
- Conduct real-vehicle application testing to ensure stable and reliable installation and performance
Production Preparation
- Correctly set the parameters and production conditions of equipment
- Verify the quality and inventory of raw materials
Mass Production
- Begin mass production and monitor product stability and quality
- Inspect dimensions, appearance, and functionality
Package Delivery
- Package products according to customer requirements
- Select the best Transportation method to ensure on-time delivery
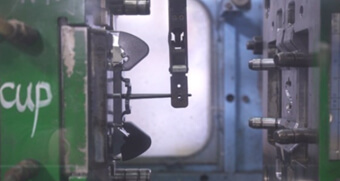
❖ Design Change Process
Design change
- After the mold development is completed or during mass production, the customer requests a design change.
Design analysis
- Analyze the feasibility of the changes that customer requested.
Quotation
- Estimate the modification cost and provide a quotation for the customer's confirmation.
Issue change- order
- If the change is confirmed, issue a design change order.
Mold modification & trial
- Modify the mold based on the design changes.
- After the mold modification is complete, conduct mold trials and sample testing.
Sample confirmation
- Customer signs back the sample if approval.
- According to the standards of confirmed sample to proceed mass production.
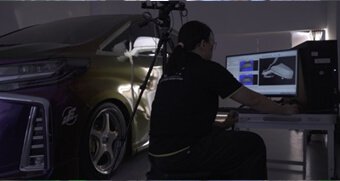