❖ Insert Injection molding
Insert Injection Molding: Embed metal or other materials into plastic for integrated molding. Suitable for electronic component housings, nut inserts, and composite structure products. As a plastic injection moulding manufacturer, we ensure high precision in embedding materials for durable and efficient products.
Prepare the insert
- Clean the surface of the insert, removing oil, dust, or other contaminants to ensure a good bond between the insert and the plastic material.
- If the insert requires higher adhesion, pre-treatment may be performed (such as roughening, plating, or sandblasting).
- Manually or automatically position the insert in the designated location of the mold, ensuring it is accurately and securely placed.
Mold installation
- Ensure the mold interior is clean and check for any damage to the mold.
- The insert can be secured in the mold using methods such as magnetism, clamps, or vacuum suction to prevent displacement during the injection process.
Materials preparation
- Select the appropriate plastic material and adjust its properties according to the requirements of the insert.
- Dry the materials to ensure the stability of the injection molding process and the quality of the product.
Injection molding
- Melt the plastic material in the heated barrel and inject it into the mold cavity using a screw to encapsulate the insert.
- Control the injection pressure, speed, and cooling time to ensure the plastic fully fills the mold cavity and properly encapsulates the insert.
Cooling Solidifying
- The plastic material cools inside the mold until it hardens sufficiently, creating a strong bond between the insert and the plastic material.
- The cooling time depends on the materials and the product structure.
Mold ejection
- Use ejector pins or an ejector plate to remove the finished product from the mold.
- When removing the part, special attention should be paid to the junction between the insert and the plastic to avoid damaging the product.
Post-processing Inspection
- Trim the product's flash and any excess parts; secondary processing may be performed if necessary.
- Check the quality, qualified products are packaged and stored, while defective ones are reworked or scrapped.
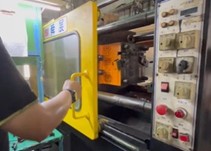
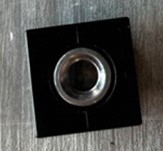