Conventional Injection molding
Conventional Injection Molding: Melt plastic and inject it into a mold to cool and form. Suitable for toys, beverage bottle caps, appliance housings, and general industrial parts. Choosing the right injection moulding manufacturer ensures consistent quality and precision in production.
Materials preparation
- Select the appropriate plastic materials for the product's requirements (such as ABS, PP, ASA, etc.).
- Dry the raw materials to prevent bubbles or defects during molding.
Parameters setting
- Set the injection molding machine's temperature, pressure, speed, and cooling time parameters.
Melt raw materials
-
Place the raw materials into the hopper of the injection molding machine, where they will be heated and melted into a flowing state inside the barrel.
Injection molding
- The melted plastic material is pushed forward by the screw under high pressure and injected into the mold cavity through the gate system.
- Control the injection pressure and speed to ensure the plastic material fills the mold cavity completely, avoiding insufficient filling or air bubbles.
Pressure holding & Cooling
- After injection, maintain pressure to compensate for the material shrinkage during cooling, ensuring the product's dimensions are accurate.
- The cooling system helps accelerate the solidification of the material.
Mold ejection
- After the plastic material has fully cooled and solidified, open the mold.
- Use ejector pins or an ejector plate to remove the finished product from the mold.
Post-processing
- Trim the product's gate and flash, removing any excess parts.
- Perform secondary processing as needed, such as printing, painting, or assembly.
Inspection Packaging
- Inspect the finished products to ensure their dimensions, appearance, and functionality meet the requirements.
- Qualified products are packaged and stored, while defective ones are reworked or scrapped.
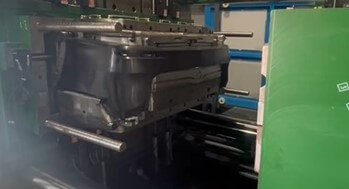
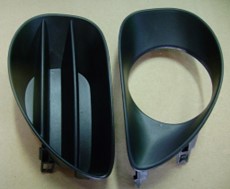